Learn how to block print to create beautiful designs
India is renowned for its unique craftsmanship. Block printing is one of these kinds of art and craft. In India block printing in states such as Rajasthan & Gujarat is predominantly practised. There are various types of printing processes in India, but the market for block print designs is so active that ever more industry wants to be able to know how to block print patterns for their fabrics.
Block printing exists on a massive scale in areas such as Bagru, Sanganer, and Ahmedabad. The artisans design the block with wooden blocks, which are tucked into dyes and afterwards imprinted on the cloth, which transforms to be a lovely pattern. The designs are colourful and beautiful. Printing of the patterns is accomplished with colours of organic products in the ancient days, but they are not. Many companies utilize natural colours. People use organic dyes, so production costs could not be raised. Yellow, black, saffron and blue are popular colours used for dyeing. The secret to printing seems to be the wooden block that is made for this purpose.
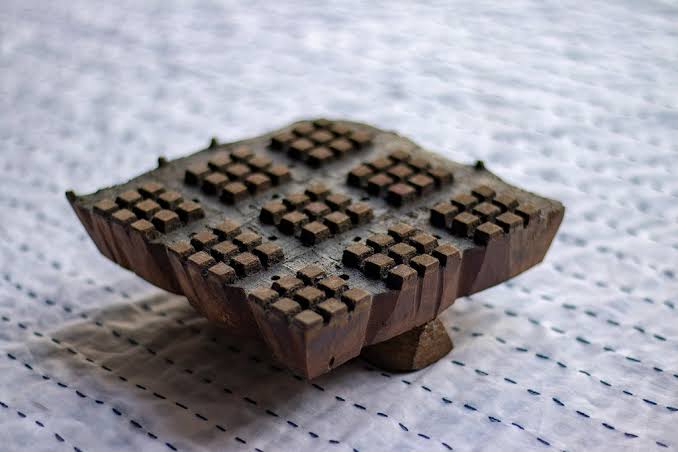
It is necessary to know that the highest care must be taken for items such as the cloth, woodblocks and colouring. Wood blocks must be dipped into the oil for at least 10 to 15 days before their use to obtain the softness required for a better impression of the pattern.
Setting the block
Wooden blocks are usually made up of sycamore, plank, or pear wood. The blocks can differ by thickness but should be 2 to 3 cm thick. The wood's side margins are intact and not sculpted. Tiny details are very hard to cut into the wood, so they usually break down when they are printed expertly. Every colour has a separate block, so it is essential to ensure that you have the same pattern before you add it while making these blocks ready. You should print the fabric until wooden blocks are finished.
The construction of the block is impressive. Such designs give a shine to the clothes to make it look appealing. In comparison to other design concepts like Phulkari, hand block printing is like many conceptual designs and mehndi designs based on the ancient art form. This hand-block printing process often makes intricate designs feasible. Some of Buti, Jhal, and Bel elements make up simple block Print designs.
Hand block printing process
Wooden blocks are so sculptured that they represent a designer's creativity. Natural geometrical shapes or more general impressions can be these hand block images. Hand-blocked designs are best moulded by designers to satisfy the needs of Indian as well as global fashion.
You must do the necessary things if you choose to go through the block printing procedure. There are several processes:
Bleaching processes:
The cloth to be used in the pattern must be combined with soda ash, cow dung, sesame oil or water. The absorption efficiency of the tissue is enhanced, and the dye is adequately absorbed.
Yellowing process:
The tissue is rolled to dissolve in the water, granting it a jaundiced hue upon completion of the bleaching process.
Printing of the block:
The woodblock first is soaked in black ink, forming a contour and then applying further colours. A blend of sticky molasses, a scrap of iron gathered from horseshoes, glue and water, creates Black Ink.
Removal of the Adhesive:
Wash the cloth in the bath to extract the adhesive that was a part of the black ink. You need to clean the fabric carefully, and after the material has been dried, it has to be discarded, and the cloth with the block written designs gets the finishing touches.
You can certainly know how to block printing from the above-described knowledge, and you can be a part of beautiful art.